In the era of Industry 4.0, robotics has emerged as a pivotal force driving automation and transforming manufacturing processes. By integrating advanced robotics into production lines, businesses can achieve unprecedented levels of efficiency, precision, and flexibility. This article explores the integral role of robotics in automation and smart manufacturing, highlighting their benefits, applications, and the future landscape of the manufacturing industry.
Understanding Robotics in Manufacturing
What Are Industrial Robots?
Industrial robots are automated, programmable machines capable of performing a variety of tasks with high precision and speed. These robots are designed to handle repetitive, hazardous, or complex operations, thereby enhancing productivity and ensuring consistent quality in manufacturing processes.
Components of Robotic Systems
- Manipulators: The robotic arms that perform the physical tasks.
- End Effectors: Tools attached to the robot’s arm, such as grippers, welders, or paint sprayers.
- Control Systems: Software and hardware that program and manage the robot’s operations.
- Sensors: Devices that provide feedback on the robot’s environment and performance, enabling adaptive actions.
Benefits of Robotics in Automation and Smart Manufacturing
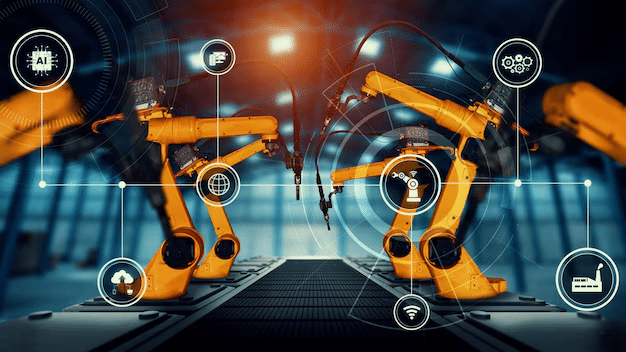
1. Increased Efficiency and Productivity
Robots can operate continuously without fatigue, significantly boosting production rates. Their ability to perform tasks faster and more accurately than humans leads to higher throughput and reduced cycle times.
2. Enhanced Precision and Quality
Robotic systems maintain consistent quality by minimizing human error. High precision ensures that products meet stringent quality standards, reducing defects and waste.
3. Improved Safety
Robots can perform dangerous tasks, such as handling toxic materials or operating in extreme environments, thereby reducing workplace injuries and enhancing overall safety.
4. Cost Savings
While the initial investment in robotics can be substantial, the long-term savings from increased efficiency, reduced labor costs, and minimized waste make robotics a cost-effective solution for manufacturers.
5. Flexibility and Scalability
Modern robots are highly adaptable and can be reprogrammed for different tasks, allowing manufacturers to quickly respond to market changes and scale operations as needed.
Applications of Robotics in Smart Manufacturing
1. Assembly Line Automation
Robots are extensively used in assembly lines to perform tasks such as assembling components, screwing, welding, and painting. Their ability to work at high speeds ensures seamless production flows.
2. Material Handling and Logistics
Robotic systems automate the movement of materials within factories, handling tasks like sorting, packaging, and palletizing. Automated guided vehicles (AGVs) and autonomous mobile robots (AMRs) optimize warehouse operations and inventory management.
3. Quality Inspection and Testing
Robots equipped with advanced sensors and imaging technologies perform quality inspections, detecting defects and ensuring products meet quality standards. Automated testing processes enhance reliability and reduce inspection times.
4. Machine Tending and Maintenance
Robots can tend to machines, loading and unloading parts, and performing routine maintenance tasks. This minimizes downtime and extends the lifespan of manufacturing equipment.
5. Custom Manufacturing and Prototyping
Robotics enable manufacturers to produce customized products with precision and efficiency. Flexible robotic systems facilitate rapid prototyping and small-batch production, catering to niche markets and personalized demands.
Integrating Robotics into Smart Manufacturing
1. Industry 4.0 and IoT Integration
Smart manufacturing leverages the Internet of Things (IoT) to connect robotic systems with other machinery and devices. This integration allows for real-time data exchange, predictive maintenance, and enhanced operational visibility.
2. Artificial Intelligence and Machine Learning
AI and machine learning algorithms empower robots to learn from data, optimize their performance, and adapt to changing environments. Intelligent robots can make autonomous decisions, improving efficiency and reducing the need for human intervention.
3. Collaborative Robots (Cobots)
Cobots are designed to work alongside humans, enhancing collaboration and productivity. They assist workers in performing tasks that require precision, strength, or repetitive motions, fostering a harmonious and efficient workplace.
4. Advanced Robotics Programming and Control
Sophisticated programming languages and control systems enable precise coordination of multiple robots, ensuring synchronized operations and seamless integration into existing workflows.
Challenges and Considerations
1. High Initial Investment
Implementing robotic systems requires significant upfront capital for purchasing equipment, installation, and training. However, the long-term benefits often justify the initial costs.
2. Workforce Adaptation and Training
Integrating robotics into manufacturing processes necessitates reskilling and upskilling the workforce. Employees need to be trained to operate, maintain, and collaborate with robotic systems.
3. Technical Complexity and Maintenance
Robotic systems are complex and require regular maintenance to ensure optimal performance. Businesses must establish robust maintenance protocols and have access to technical expertise.
4. Data Security and Privacy
With increased connectivity, robotic systems are vulnerable to cyber threats. Ensuring robust cybersecurity measures is essential to protect sensitive manufacturing data and prevent disruptions.
The Future of Robotics in Smart Manufacturing
1. Enhanced Autonomy and Intelligence
Future advancements in AI and machine learning will enable robots to achieve higher levels of autonomy, making them more intelligent and capable of performing complex tasks without human intervention.
2. Increased Collaboration with Humans
The development of more sophisticated cobots will further enhance human-robot collaboration, creating more efficient and versatile manufacturing environments.
3. Sustainable and Green Manufacturing
Robotics will play a crucial role in sustainable manufacturing by optimizing energy usage, reducing waste, and enabling eco-friendly production processes.
4. Integration with Augmented Reality (AR) and Virtual Reality (VR)
AR and VR technologies will complement robotics by providing immersive training experiences, real-time monitoring, and enhanced control over manufacturing processes.
5. Global Standardization and Interoperability
Efforts towards global standardization will facilitate the interoperability of robotic systems across different platforms and industries, promoting widespread adoption and innovation.
Conclusion
Robotics is at the heart of the automation and smart manufacturing revolution, driving significant advancements in efficiency, precision, and flexibility. By integrating robotic systems into their operations, businesses can achieve higher productivity, enhanced quality, and improved safety, while also positioning themselves for future growth and innovation. Despite challenges such as high initial costs and workforce adaptation, the benefits of robotics in manufacturing far outweigh the obstacles. As technology continues to evolve, robotics will play an increasingly vital role in shaping the future of manufacturing, fostering sustainable and intelligent production environments.
FAQs
1. What is the difference between industrial robots and collaborative robots (cobots)?
Industrial robots are typically large, powerful machines designed to perform repetitive and heavy-duty tasks in manufacturing settings. Collaborative robots, or cobots, are designed to work alongside humans, assisting with tasks that require precision and adaptability, enhancing human-robot collaboration.
2. How can businesses afford the high initial costs of robotics?
Businesses can offset the high initial costs by considering long-term savings from increased efficiency, reduced labor costs, and minimized waste. Additionally, leasing options, government incentives, and phased implementation strategies can make robotics more financially accessible.
3. What skills are required to manage and maintain robotic systems?
Managing and maintaining robotic systems requires skills in robotics programming, mechanical and electrical engineering, data analysis, and cybersecurity. Additionally, training in operating specific robotic platforms is essential.
4. How do robotics improve product quality in manufacturing?
Robots enhance product quality by performing tasks with high precision and consistency, reducing human error. Their ability to maintain exact specifications ensures that each product meets quality standards, leading to fewer defects and higher customer satisfaction.
5. What role does AI play in the advancement of robotics in manufacturing?
AI enhances robotics by enabling intelligent decision-making, adaptive learning, and predictive maintenance. Machine learning algorithms allow robots to analyze data, optimize their performance, and adapt to new tasks, making them more autonomous and efficient in manufacturing environments.